The very idea of the ESA Business Incubation Centre is conveyed in our favourite hashtag: #downtoearth. Start-ups are challenged to use space technology to solve a problem on earth. Johan Leijtens from alumnus Lens R&D did just that. And then he took his technology back #uptospace.
The company Lens R&D, which celebrated its fifth birthday last year, develops “space-grade, off the shelf” sun sensors. This week, Lens’ brand new office and clean rooms were officially opened right across the street from the SBIC Building.
Space sensors for renewable energy
Lens R&D was founded in 2012 by Johan Leijtens, based on many years of experience as a systems engineer developing sun sensors. His original idea for Lens was using space-grade sun sensors for large concentrated photovoltaic (CPV) installations. However, he could not completely give up his love for space, so in parallel he kept working on sensors for space applications.
This turned out to have been a smart decision when the CPV market collapsed in 2015 as solar panels became much cheaper. At the same time, large orbital constellations such as the OneWeb project made the small satellite market boom.
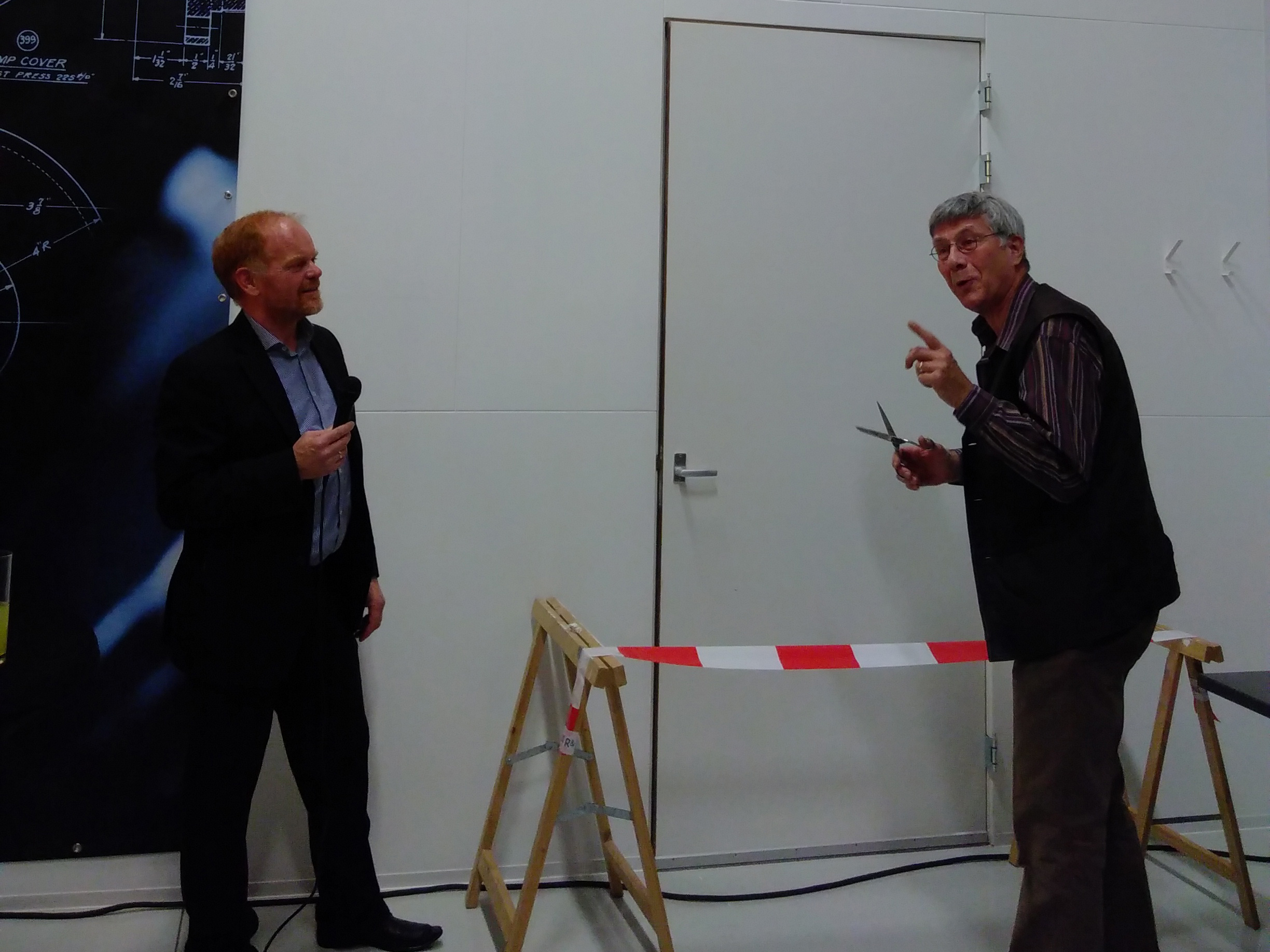
“Mr Sunsensor” Kees de Boom gives some sound advice to Johan Leijtens before cutting the ribbon to open the clean rooms.
Smallsat constellations
“I cannot say that I completely predicted these large constellations,” Leijtens admits. “But during my time at TNO, I did see that small satellites were going to become important. That is one of the reasons I left to start my own company.”
Small satellites have very different requirements than the 250+ million euro satellites that need to operate perfectly for decades. “Smallsats also need to work well, but at a different cost. So, you will have to change the way you control the quality and provide documentation, and make it cheaper without affecting the reliability.”
Off the shelf
Lens R&D is unique in the space sector, because it aims to provide these space-grade sun sensors off the shelf (OTS). “In the USA, so-called recurring production is already common,” Leijtens explains. “But that is not literally off the shelf, they are still produced per project. We build 50 or 100 sensors in one batch, which reduces the cost per sensor significantly.”
The OTS approach requires a different attitude from potential customers like ESA or Airbus – they can no longer make individual requirements for every project. But most importantly, it requires the producer to take quite a bit of (financial) risk. “It means we have to have a lot of faith in the quality of our product. It’s a risk that we are starting to master.”
The newly constructed clean room similarly shows Lens’ stubbornly unique approach. A standard model clean room was unfeasible financially, so the Lens team built their own: the first wooden clean room in the Netherlands. Over the next couple of weeks, inspections will have to prove that this works just as well as a standard model clean room and that it meets all certification demands.
Business potential
Over the past couple of years, Lens R&D worked closely with ESA and NSO to produce fully qualified sun sensors. “But ESA only launches one satellite per year. Our real business case lies in mass production for private satellite builders,” Leijtens predicts.
“This market did not exist yet in 2012, but now constellations are starting to boom, and we have a head-start of 4 or 5 years over our competition.”