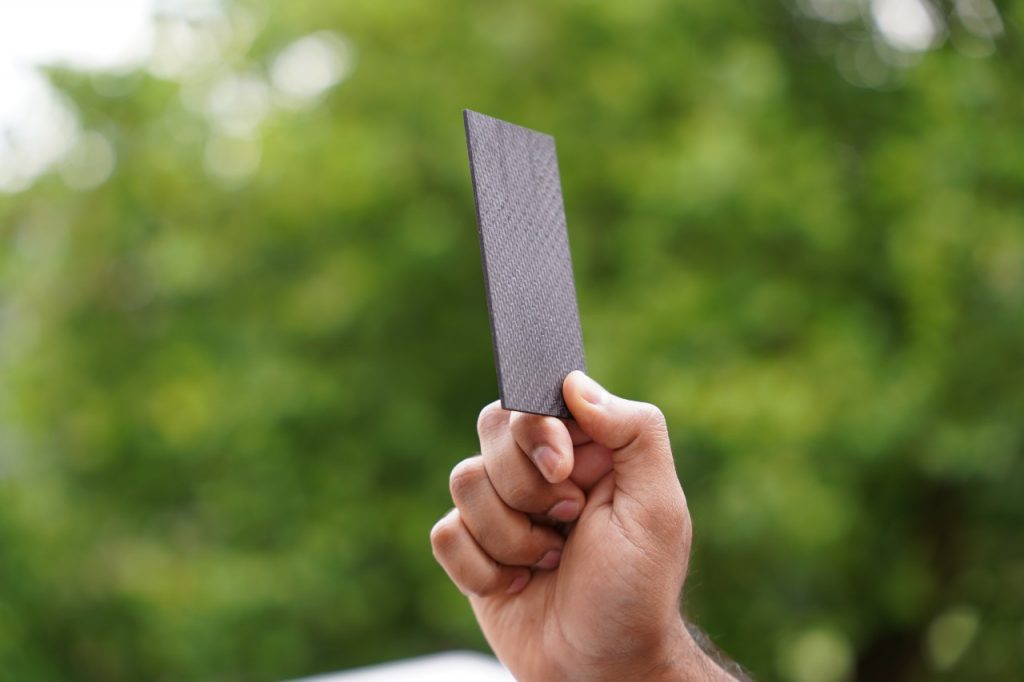
In the space industry, weight is king. Ideally you’ll want materials to be as light as possible, while being strong and cost-friendly at the same time. Enter Arceon, a startup in ESA’s business incubation programme in Noordwijk, that develops high-potential materials suited for industries with harsh conditions like space.
Arceon is developing ceramic matrix composites to improve materials and structures. These can be used in the production of satellite thrusters, sounding rocket motors and thermal protection systems. Next to that, the company is making products themselves.
We talked to two of the co-founders, Rahul Shirke (CEO) and Rahul Sharma (COO), about their novel materials and the impact they could have on the space industry.
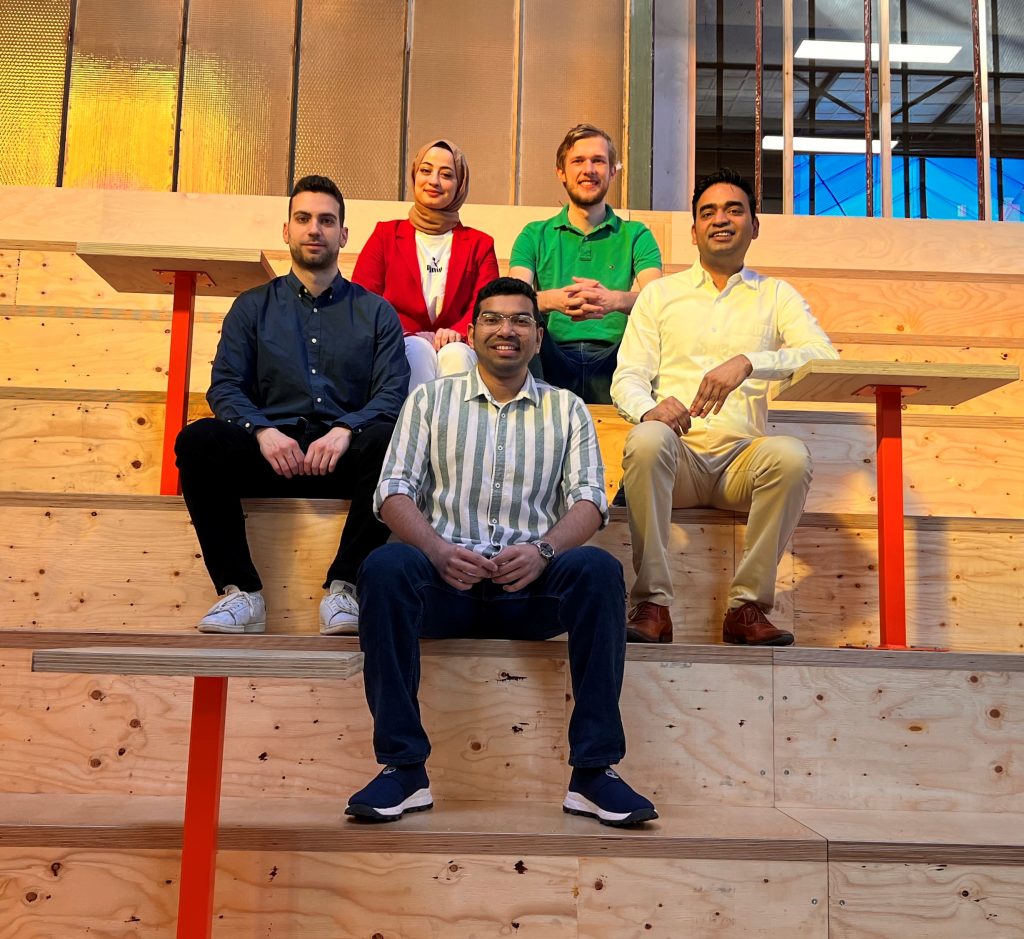
What problem does your company solve?
Rahul Shirke: “Propulsion systems are restricted by the thermal limitations of the metals. This leads to a lot of thrusters not reaching their full potential. We enable that potential by reducing the mass – our material is 4 times lighter than the metals that are used currently. At the same time we are able to increase the temperatures themselves in space propulsion systems, so we are increasing efficiency in multiple ways. In the end, we will be able to say we are 3 times more efficient than other current systems. And, of course, while matching the costs of the metals used right now.”
How do your composites work and how do you make them?
“For starters, we don’t make coatings to improve materials, we make the composites for the materials. So the resistance and the properties that make it efficient – that can take high thermal loads – are in the material itself.
How do we make it? There are three steps. First, we mould raw material and our trade secret resin in any complex shape. Second: we heat that material through pyrolysis, which decomposes the material and removes some volatiles. What’s left is then a porous carbon material called ‘carbon-carbon’. Step three is infiltrating silicon. It’s not a carbide yet. When the silicon melts, it’s sucked inside the material because of the porosity. And that gets chemically converted into silicon carbide.”
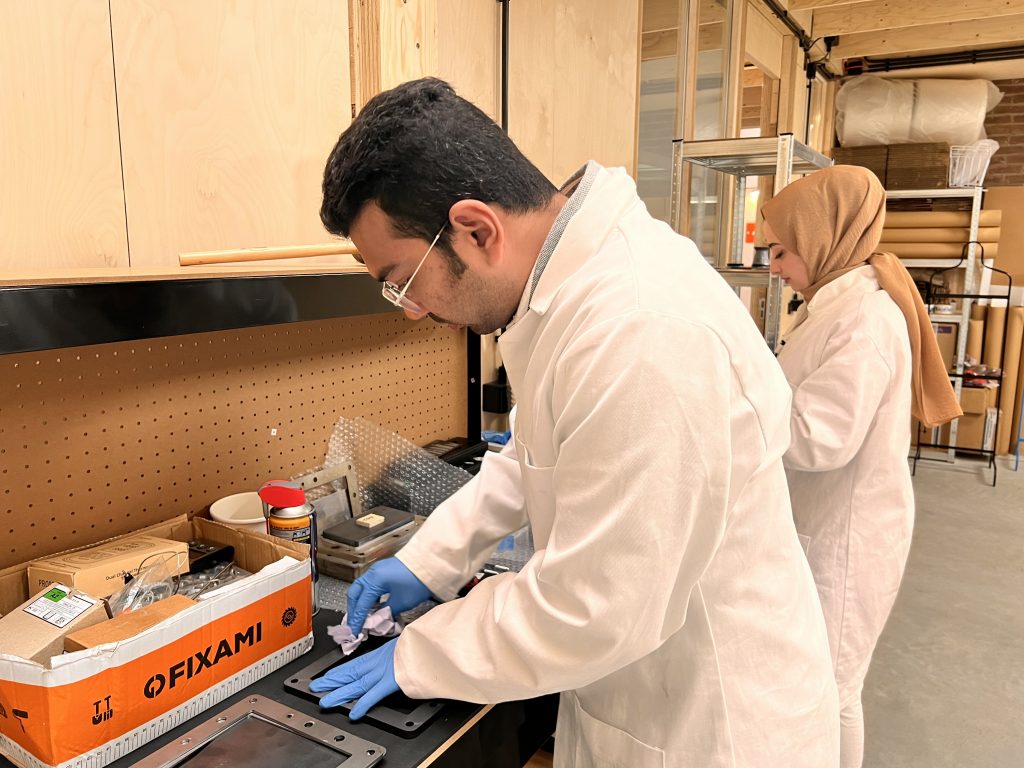
What applications are there for the materials?
Rahul Sharma: “For the space industry, think of the satellite thrusters, sounding rocket motors and thermal protection systems. But in general, we like extreme environments. So we also have purchase orders from the nuclear and refractory industry. Our most developed material is a carbon ceramic at TRL 7.”
Are you thinking of other applications in space as well?
Rahul Shirke: “There is one application we are not focussing on right now, but in the end our same material can be used for optical systems in space as well. Composites can fly in space, but cannot be used near optics. That is because normally due to outgassing, some material will settle on the optics as time passes by – which reduces the efficiency of laser systems and optical communications. You can imagine that the James Webb telescope needs to be clean! Our material has near zero thermal expansion, and zero outgassing. Next to that, our density is 25 percent lighter than aluminum.”
Rahul Sharma: “Currently, mirror holders or baffles for optical systems are made out of aluminum or titanium which needs to be painted black if you don’t want any light reflected into the sensors. That paint also adds to the weight and cost. Our material is already black.”
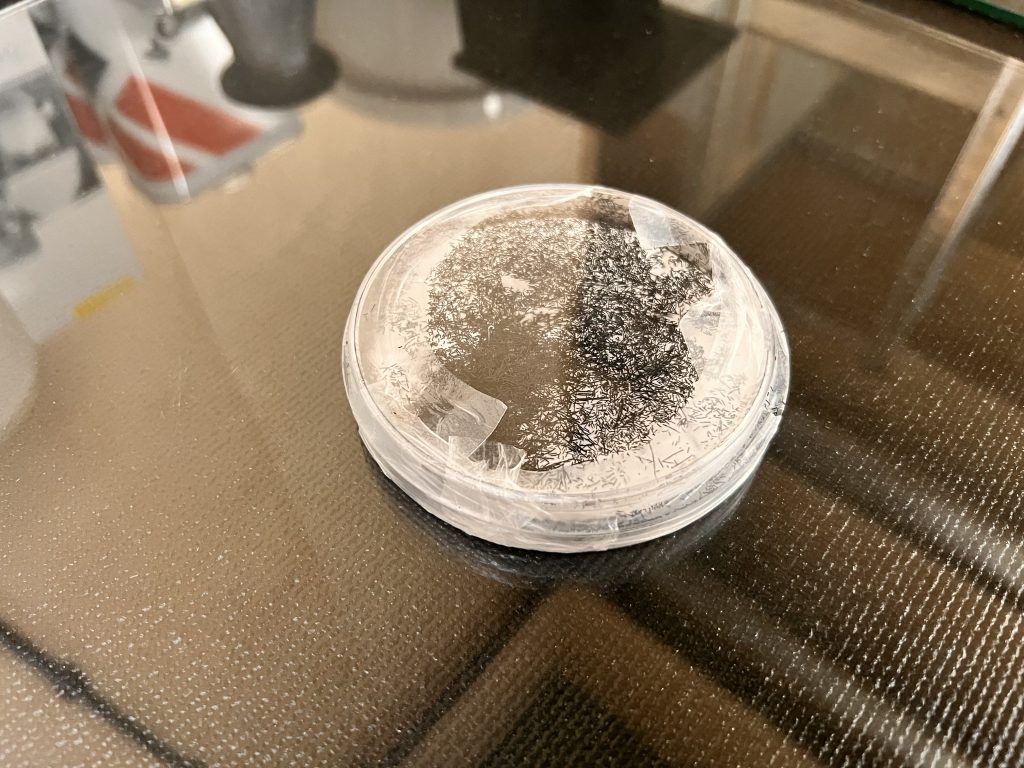
How did Arceon came to be?
Rahul Shirke: “I worked on the structure of our material with Bernard Heidenreich, a researcher with 30 years of experience, now our CTO. That’s where I first learned from it. No-one was doing it at the time. I noticed the material has huge potential – so I immediately thought of ways on how to commercialize it. In November 2018, we officially started Arceon and Rahul Sharma then quickly joined. The first thing I needed to do was to take costs down by making the process optimized – while not compromising on the quality.”
Rahul Sharma: “We both graduated the same year from TU Delft. After that I worked as a product engineer. So when I was asked to join, the idea of the composites was exciting to me. Plus, working in a startup drove my interest. My role here is to make processes and handle project management, so we go in the right direction.”
What does the name Arceon mean?
Rahul Shirke: “Arceon is a composition of ‘arc’ and ‘eon’. ‘Arc’ is a pinnacle you’ll see in measurements and ‘eon’ the timespan that you cannot measure. So combined, you’ll get something like ‘peak and never ending’ – a meaning we want to apply to our business. So we found ‘Arceon’ really fitting.”

What are some challenges you see right now?
“Our customers mostly use superalloys or metal alloys on their material. It’s been used for years, it’s everywhere. So you can imagine changing that to what we propose can be challenging – even if it gives you efficiency and less costs.”
Rahul Sharma: “In the space industry, data is really important, so we must test our solution in different environments and conditions first and convince the customer. We must be able to show certified end tests. The test results will be available on our website for the customers.”
Can you describe both your short- and long-term goals?
Rahul Shirke: “Our short-term goal is to build a product portfolio in 3 sectors: space, defense and industry. In the long-term, we want to scale-up by expanding to multiple industries and diversify our portfolio. Think of the automotive industry – they need thermal management of batteries. Think of aviation. And the marine industry needs corrosive resistance material that has a high load carrying capacity and high compressive strength.”
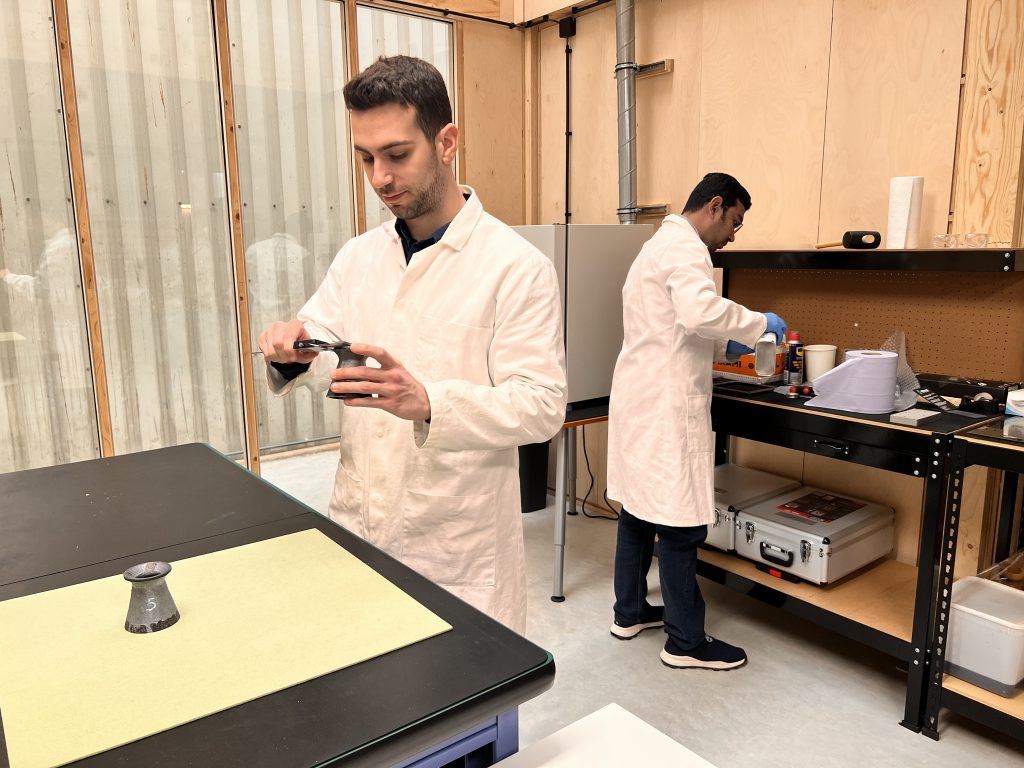
What are you proud of so far?
“We got selected by ESA to board our materials on the Bartolomeo platform that will be connected to the International Space Station. Our materials will be exposed to the conditions of space, outside the ISS, for a period of 6 months to a year, to study it for future projects.
A preliminary test on the materials by ESTEC (ESA’s R&D facility located in Noordwijk) showed two orders of magnitude lower erosion yield than normal carbon fiber polymers. There was so little erosion it was almost negligible. Those are some good results we hope to repeat in space.”
Why did you choose to be in the ESA BIC programme?
“First of all for us it was about the vast network – you’ll get to know the space industry better this way. Now we are in ESA BIC, the advisory and regular meetings within the programme are really helpful as well, because they push us in the right way.”
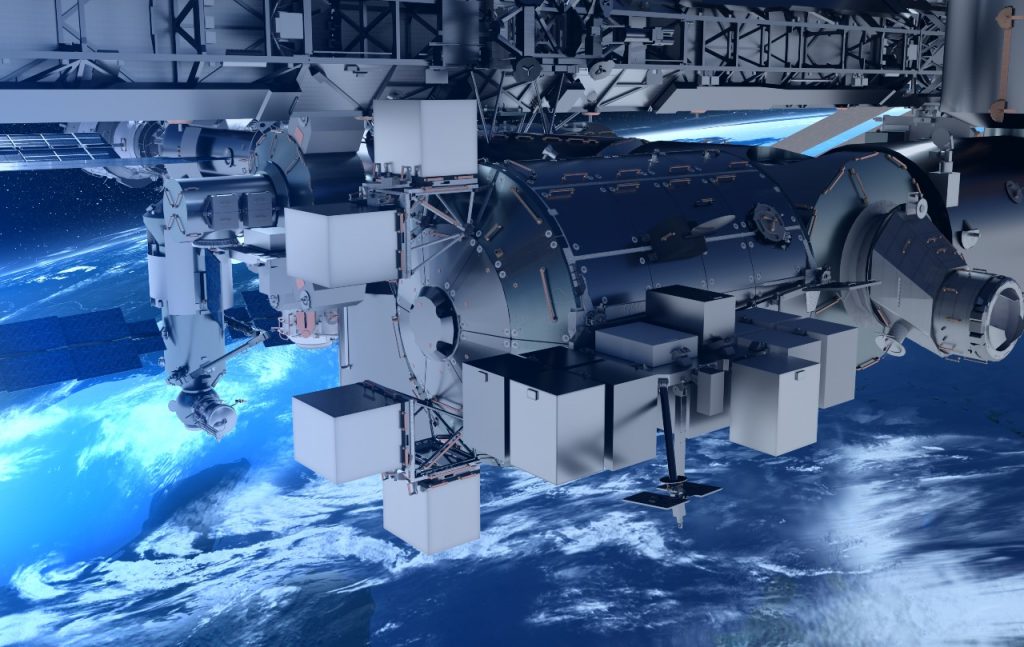
What advice would you like to give other entrepreneurs?
“Take the leap of faith and don’t wait for the right time to do things. Just do it. It’s a rewarding process. Whatever the outcome, you will go through some cycles which will teach you a lot for you as a person and as an entrepreneur. Also: know your strengths and weaknesses, and hire accordingly.”
Rahul Sharma: “One of the major challenges for any startup is finance. There are a lot of funding and subsidy opportunities available. You just need to talk to people around you, like we do here in the ESA BIC Noordwijk programme. It is here we learned from other entrepreneurs about certain funds from the local government.
While Arceon literally has a secret ingredient, both co-founders also acknowledge their team as a strength. “It’s a complementary and capable team that has an answer to nearly every question. That’s why we are so confident we can handle any extreme environment.”